皆さま、こんにちは、管理人です。
製品化学物質管理における経験や事例シリーズの第5回目です。
このシリーズは、2002年1月(もしくは、2001年11月or12月)から製品化学物質管理に関わってきた管理人が経験したことや事例を書いていくものです。
さて、今回のお話は、製品化学物質管理における経験や事例(その2)では、色々問題があるので書かないとした、社内で製造した製品のRoHSへの対応のお話です。
本当に細かいところはもちろん書けないのですが、15年以上経ったことですし、大丈夫かなという範囲で書いていきたいと思います。
RoHS指令への対応をする製品
RoHS指令は、欧州の電気電子機器を対象とする規制なので、2006年の7月時点では欧州向けの製品だけ対応すればいいはずです。
ですが、会社の方針は、「基本全製品RoHS指令に対応する!」でした。
なんでそんな大変なことをするんだと思う方もいるかもしれません(というか普通はそう思うでしょうね)。
理由はいくつかあります。
- 会社における売り上げの日本地域の割合は、全体の1/4以下しかない
- RoHS指令に類似した規制が、他の国でも検討されているようだ
- 仕向け毎に汎用部品を変えるわけではない
- 仕向け毎に管理をする方が大変
一旦、RoHS指令に対応しておけば、他の国でRoHS類似の規制が来てもやることは最小で済みますし、新製品を作るにしても同じルールにしておけば、それさえクリアすれば自由度が高くなります。
以上のような理由から、RoHS対応は全製品対応、製品化学物質管理における経験や事例(その1)で書いた技術標準(SS-00259)は、これらを見据えて改版を重ねていったのです。
FIFO管理の徹底をしないとえらいことになる
RoHS指令の施行開始は、2006年の7月からでした。ですので、それまでに欧州域内に上市する製品はRoHS指令に対応した製品を製造し送り込まなければなりません。
更に、以前に製造されRoHS指令を満たしていない製品については、期日までにそれを上市(利用可能な最初の状態)までもっていかなければなりません。
そこで出た指示が、期日までにRoHS未対応品を売り切れというものでした。
(多分今でもRoHS指令とREACH規則では上市の定義は微妙に違うはずです。)
このような状態になっとき皆さんの会社ではどうしますか?
やり方はきっと色々あると思います。
例えば、やり方その1
性能的には全く同じ製品でもRoHS対応品は、型番もしくは社内コードを変えてしまう。
やり方その2
シリアルNo.で管理をする。
やり方その3
RoHS未対応品と区別するためにRoHS対応品には、一定期間マーキングをする。
などなどです。
どの様な方法を取ろうと必要なのは、FIFO(先入先出)管理です。これで来てないと工数的な無駄がえらいことになります。
ところが実際の倉庫においては、なかなかそうもいかないです。2006年当時ということもあり、今のようにすべてITで管理できるほど完全ではないところがあったのも事実です。作業現場における事情もあります。
ただ、このおかげで、不良在庫や端数在庫というかそういうものを一掃できたのも事実かもしれません。
RoHS対応製品を作るには、部品全部がRoHS対応部品でなければならない
RoHS対応製品を作るには、部品全部がRoHS対応部品でなければなりません。
いやいや、そんなの当たり前でしょうと言われるかもしれませんが、いわゆる電気電子機器は往々にして何百、何千もの部品で作られるのが普通です。
その部品全部がRoHS対応しているかどうかは、特に過渡期にあたっては調べるのは非常に大変です。
ですので、製品化学物質管理における経験や事例(その4)で説明したようなDBが必要になってきます。
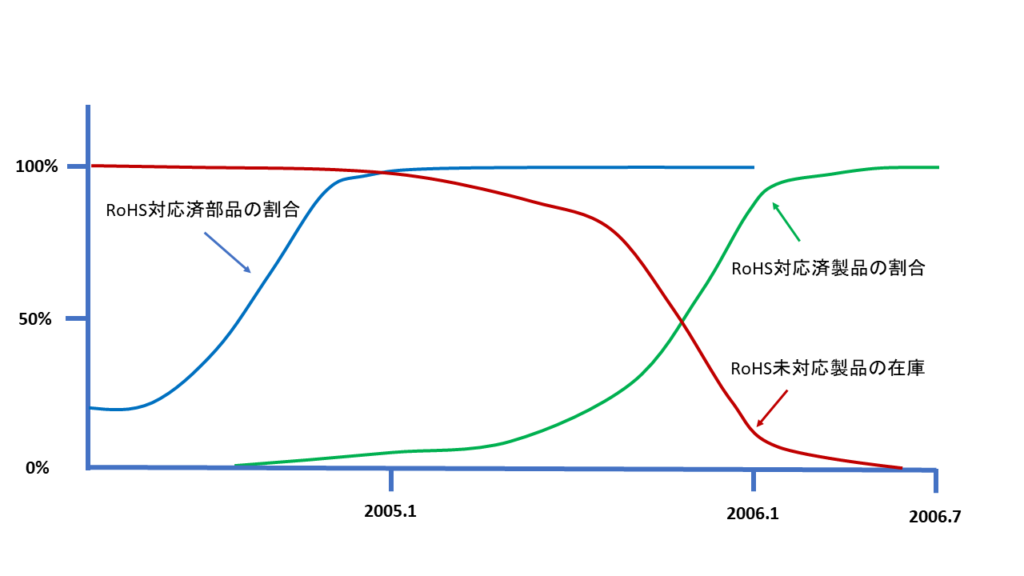
上の図は、部品と製品の当時のRoHS対応をイメージ化したものです。横軸に時系列があり、縦軸は、RoHS対応が済んだ部品および製品の割合を示しています。そして、RoHS未対応品の在庫の量が示されています。
2005年に入ると部品はほぼ100%RoSH対応されていますが、製品で対応済みのものはごくわずかです。これは、部品の在庫もあるために、全ての部品がRoHS対応のものに切り替わるためにはリードタイムが必要なるからです。
これらを実際に規制の施行日までモニターし管理し、未対応製品を売り切るというオペレーションが行われたのです。(管理人、当時を思い出すだけでくらくらする(^^;)
社内にも抵抗勢力はいる
こういう仕事をするとろくでもない言われ方をしたり、言うことを聞いてくれなかったりする人が必ず出てきます。
えっ?皆さんの会社にはいない?、うっそー!それは本当にいい会社ですね。
まあ、利益に直結するわけではありませんからね。ですけれど、それをほおっておくと会社としてのリスクは上がっていきます。
意を決して諫めに行きましょう、そして理解してもらいましょう。と、その前にこういう法的な対応、およびそれを基にした顧客からの要求については、経営層の理解とお墨付きを得ておくことが最も重要です。
ろくでもないことを言ってくる人や、言うことを聞いてくれなかったりする人って往々にして、理解してくれるとすごく強い味方になってくれたりします(管理人の過去の経験から)。時間をかけてでも説明するのが吉です。
ということで、今回は会社の中での対応をすごーく丸めて書いてみました。
コメント
お久しぶりです。
毎回、興味深く体験談を読ませて頂いています。
今でこそ、RoHS非対応の部品はPVC関連を除くと珍しくなりましたが、規制がスタートする前後はさぞや大変だったことと推察します。前回の51%の理解というお話にもご苦労が伺えましたが、この手の話は、今の若い人には理解しにくいのかもしれませんね…
このような先人の苦労があって、今があると言うのは忘れないようにしたいものです。
これからも経験談に期待しています!
通りすがり様、コメントありがとうございます。管理人です。
読んで、共感していただける方がいると本当にありがたいです。このシリーズ、書き始めた割にはコメントなど反応が薄いので、もはや必要ないのかななどと思っていたところです。
何でもいいからリアクション欲しいですー。くれくれマンになっている管理人(^^;。
今は、情報が満ち溢れているし、ITの発達に伴って管理もだいぶ楽になったでしょうし、もっと言えば他のリスク(セキュリティリスクやコンプライアンスリスク)の比重のほうが圧倒的に高くなってるのかもしれません。
昨日の吉野家の件なんてその典型ですからね。
このシリーズ、リスクにぶち当たった時にどうするのかという面から読んでいただいても良いのかもしれません。
とは言え、化学物質の規制も増えこそすれ減ることはないので、注意しましょう。